Milling is a crucial metalworking technique involving the use of rotating blades to precisely cut fixed workpieces, and it's widely applied across various industries. From cutting engine parts to processing molds, milling is indispensable in manufacturing modern products and industrial equipment components.
It is not only vital for creating precision metal parts but also plays a key role in enhancing machining accuracy.
Understanding each aspect of the milling process is essential for improving the overall quality of metalworking.
This article will provide an overview of the milling process, how it differs from other metalworking techniques, and the various types of milling methods and tools used.
Through this approach, a deeper understanding of milling's critical role and applications in modern manufacturing can be gained.
What is milling?
Milling is a precision machining technique that uses a rotating cutting tool, such as a mill or end mill, to shape stationary workpieces into complex geometries.
This process is ideal for fabricating square parts, gears, molds, and mechanical components.
Milling machines come in two main types: vertical, where the tool spindle is perpendicular to the workbench, and horizontal, where it is parallel.
This versatile method, part of the "removal process" category, efficiently removes unwanted material to achieve the desired shape.
Known for its high-precision capabilities, milling is extensively used in various industries for creating flat surfaces, curves, drilling, and slotting.

Known for its high-precision capabilities, milling is extensively used in various industries for creating flat surfaces, curves, drilling, and slotting.
What is the difference between milling and turning?
Milling and turning (lathe) are two typical cutting processes, with key differences lying in the rotation of the workpiece and the tool, as well as their machining specializations.
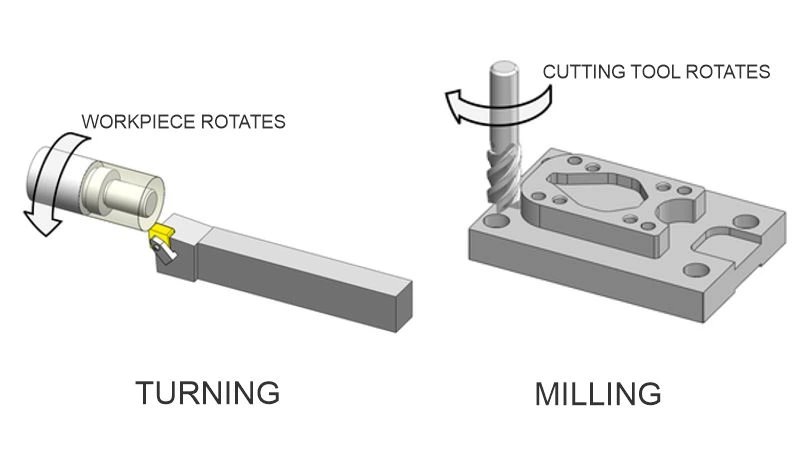
Rotation of Workpiece and Tool
In milling, the cutting process is executed by applying a rotating cutting tool to a fixed workpiece.
In contrast, turning characterizes the fixation of the cutting tool onto a rotating workpiece.
Therefore, milling involves a combination of a fixed workpiece and a rotating tool, whereas turning involves a fixed tool and a rotating workpiece.
Types of Cutting Tools Used
Milling typically employs specialized tools like end mills and face mills, while turning uses tools known as cutting inserts or tool bits.
Machining Specializations
Milling excels in machining flat surfaces and straight grooves, suitable for complex shapes and precise cuts; turning, on the other hand, is adept at machining cylindrical objects, such as the external circumference and internal surfaces, making it suitable for round-shaped workpieces.
In summary, milling and turning each have their strengths in the field of metalworking, and their application depends on the specific requirements of the machining task and the shape of the workpiece.
Commonly used equipment for milling
Milling machines, essential in modern manufacturing, come in various forms, each tailored for specific tasks and levels of precision.
Universal milling machines
Universal milling machines are manually controlled, where the operator adjusts the spindle and workbench to manipulate cutting tools.
The quality of work largely depends on the operator's skill, making these machines ideal for crafting unique items and prototypes.
They are categorized into vertical and horizontal types, based on the spindle orientation.
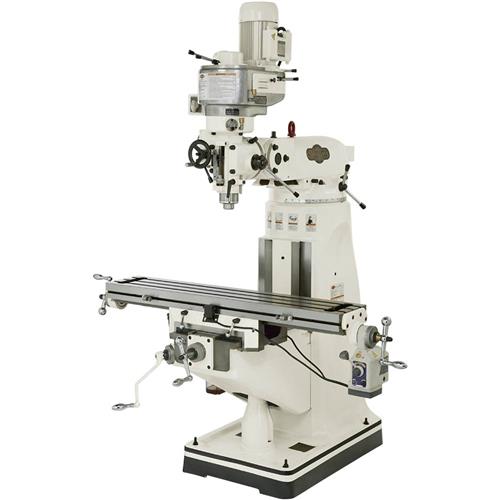
Numerical Control (NC)
Numerical Control (NC) milling machines automate the milling process by quantifying spindle and workbench coordinates, processing conditions, and machine movements.
Most modern NC machines are computer-controlled, known as CNC milling machines, offering precision that doesn't rely on operator skill.
The key advantage of CNC milling is its automation, ensuring consistent quality.
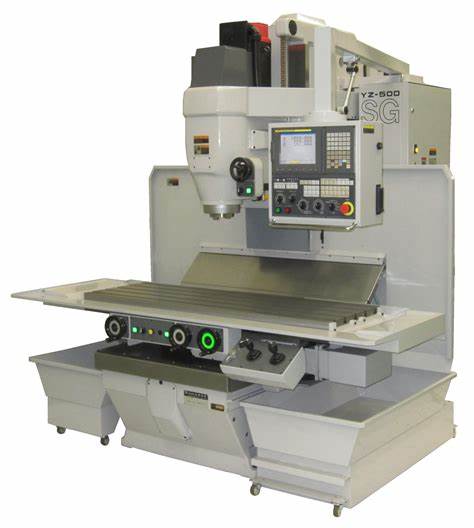
Machining centers
Machining centers, an advanced form of CNC milling machines, include Automatic Tool Changers (ATC), eliminating the need for manual tool changes and enhancing efficiency.
Multiaxial multitasking machines, capable of changing the spindle and workpiece orientation on multiple axes, allow for even more complex and intricate machining processes.
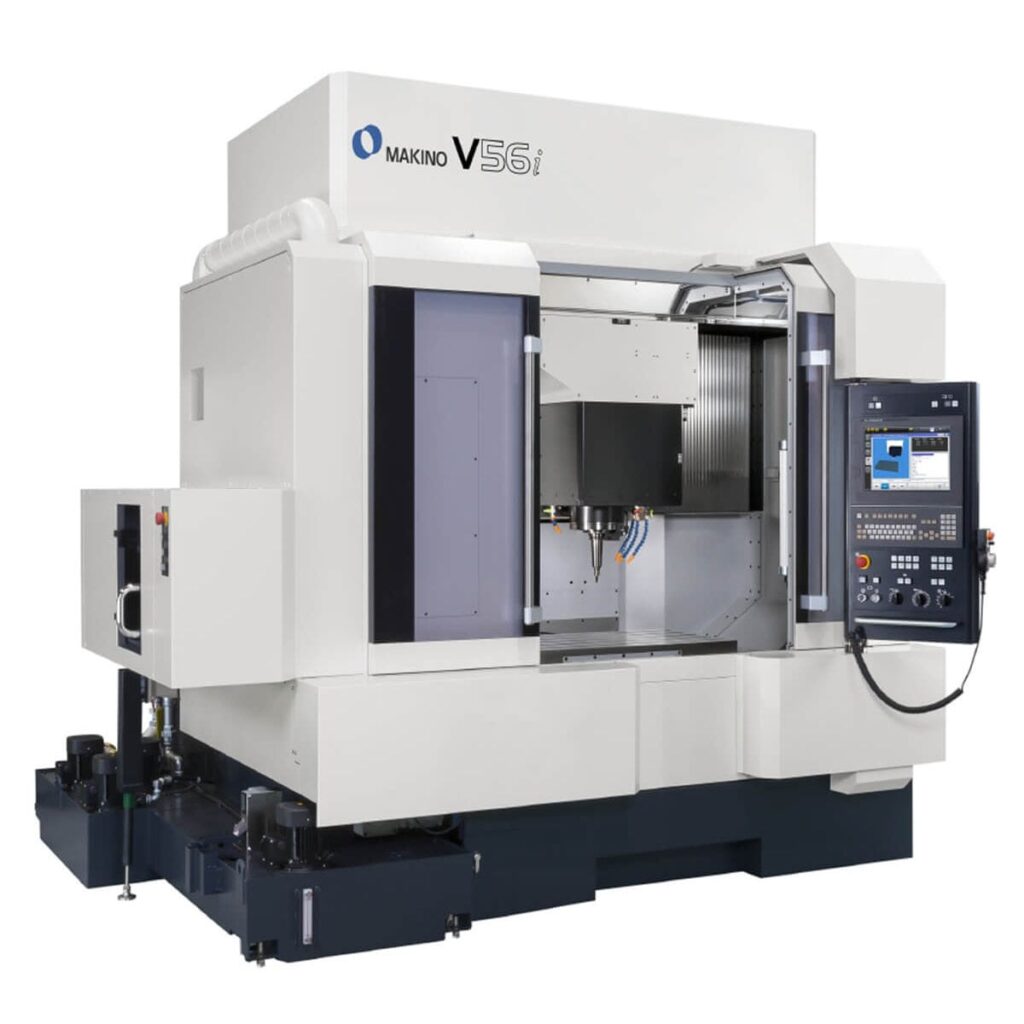
Each type of milling machine contributes uniquely to the manufacturing industry, from manual precision of universal mills to the automated, complex capabilities of machining centers.
What are the milling cutters?
In milling, various types of milling cutters are used, each designed for specific machining tasks and material shapes.
Face Milling Cutters
These cutters have multiple cutting edges around their circumference, used for efficiently cutting the surfaces of workpieces.
They typically use replaceable and interchangeable disposable cutting edges, and to reduce vibration caused by cutting forces, designs like unequal spacing and unequal lead are employed.
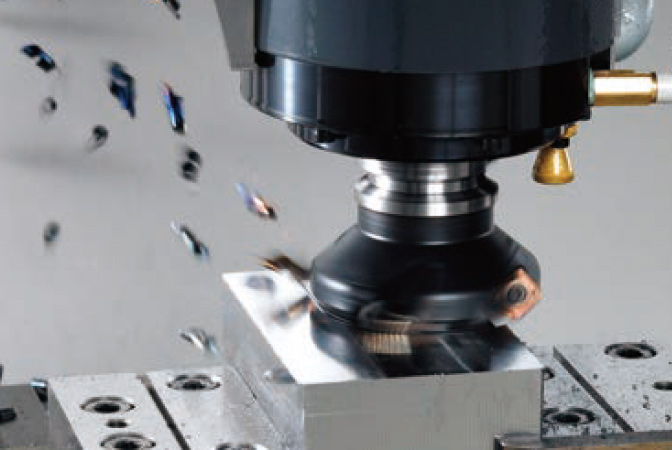
End Mills
Characterized by their elongated shape, similar to drill bits, end mills can process not only the periphery but also the bottom of the workpiece.
They are versatile tools suitable for tasks like flat machining, step machining, and groove cutting.
End mills can machine fine shapes on small areas and allow for the replacement of various types of blades as per the requirement.

Slot Milling Cutters
These disc-shaped milling cutters have cutting edges on their circumference and are used for cutting straight grooves and slots.
Particularly suitable for processing a large number of long and deep grooves, they offer faster and more precise cutting compared to end mills.

Plain Milling Cutters
Cylindrical in shape with cutting edges on their circumference, these are mainly used for rough machining, especially on horizontal milling machines.
While they have high cutting efficiency, their accuracy is less compared to face milling cutters.
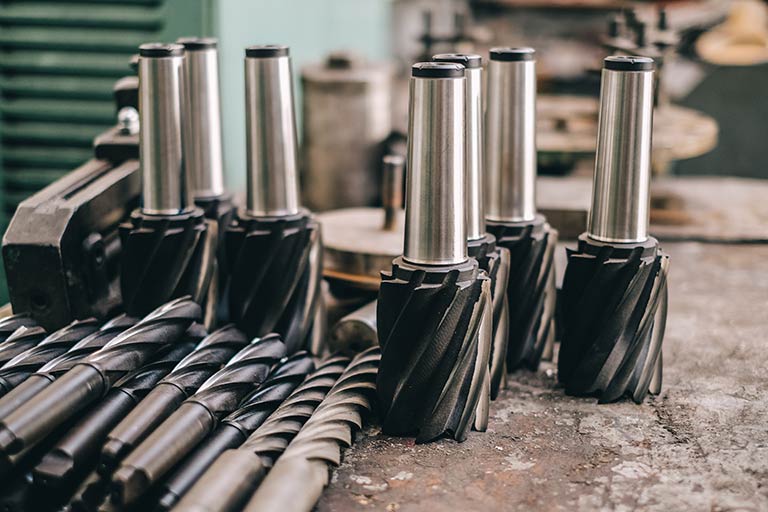
Side Milling Cutters
Disc-shaped cutting tools with cutting edges on both their circumference and sides, mainly used for side machining and slotting on horizontal milling machines.

In summary, the choice of a milling tool depends on the specific requirements of the machining task, such as the size of the cutting area, the complexity of the shape, and the required precision of machining.
Each type of milling cutter has its unique functionality and application, making milling a highly flexible and precise machining method.
What are the milling processes
Milling encompasses a variety of processes, each utilizing different tools and techniques for shaping materials.
Here's a consolidated summary of the primary milling methods:
Flat Surface Milling
This process involves cutting a workpiece's flat surface.
The technique varies based on the milling cutter used, typically employing face milling cutters for large surfaces and end mills for smaller areas.
Vertical milling machines use face milling cutters, while horizontal machines are suited for plain milling cutters.
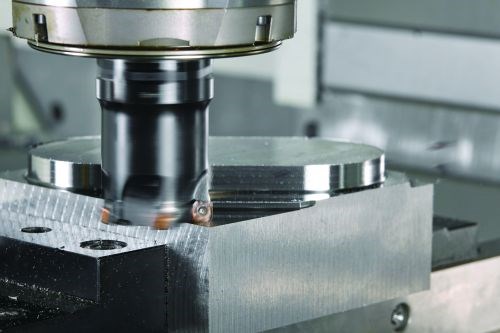
Side Milling
Here, the tool moves vertically to cut the sides of the workpiece.
Common tools include face and end mills, with side cutters also used on horizontal milling machines for roughing operations.
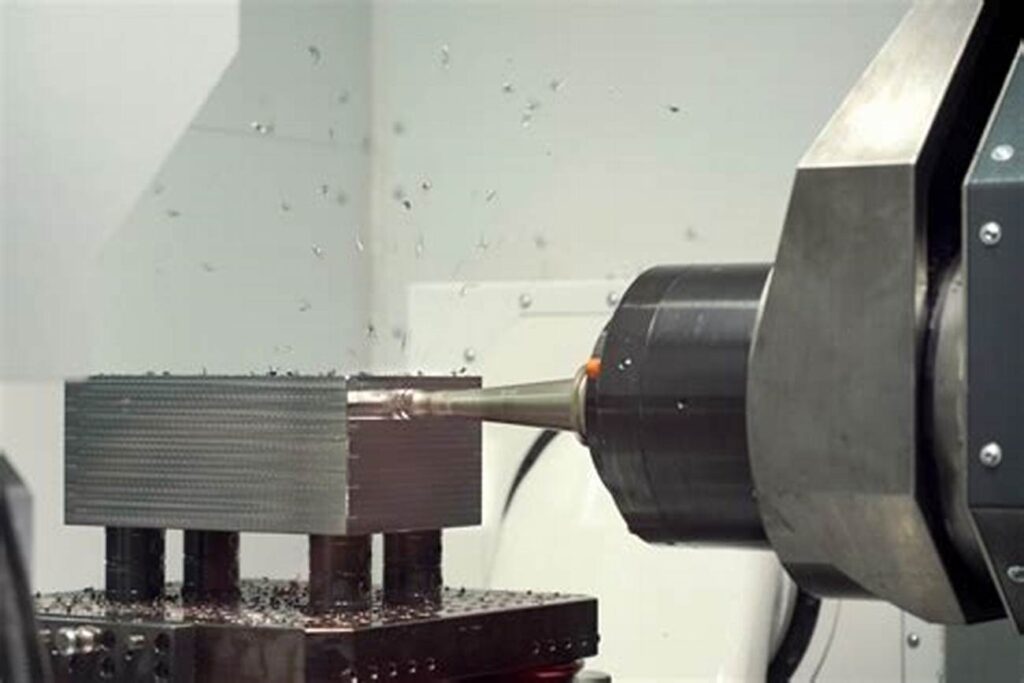
Step Milling
This method cuts both flat surfaces and sides simultaneously to create steps. Wider surfaces and lower steps are machined using face milling cutters, while narrower surfaces and higher steps are handled with end mills.

Slotting
Slot milling creates grooves in the workpiece. This process typically uses end mills and slot milling cutters, with the work table moving to cut the groove to the desired depth. T-slot cutters are used for wider bottom grooves.
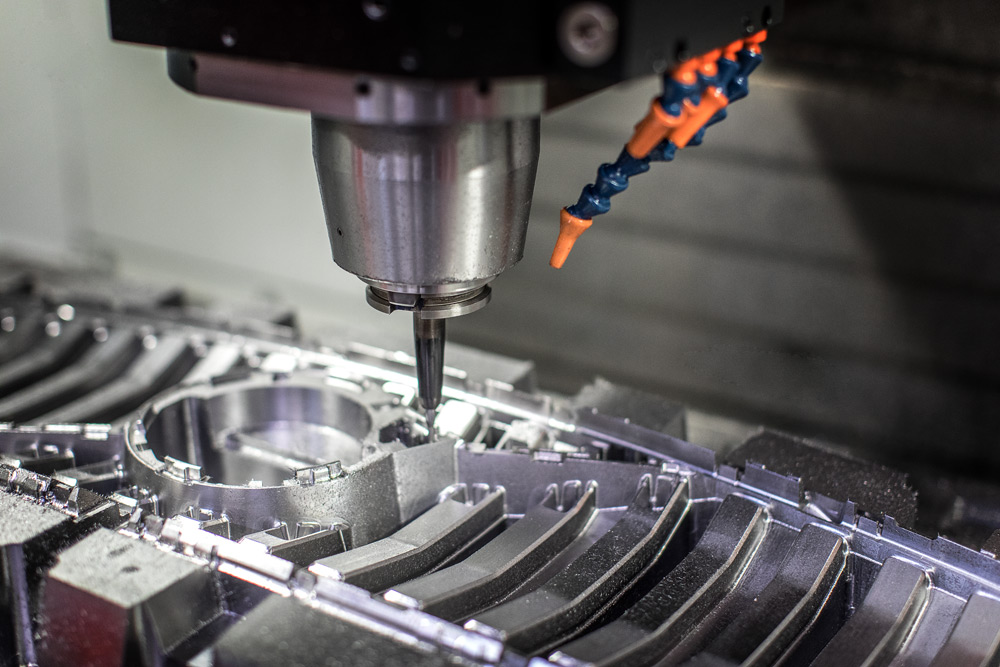
The next text describes various specialized grooving processes in milling, each tailored for creating specific types of grooves and applications:
T-Slot Milling
This process involves creating T-shaped grooves on workpieces, commonly used for securing bolts, such as on the tables of machining centers. T-slot milling cutters are specifically used for this purpose.

Dovetail Milling
Dovetail milling produces dovetail-shaped grooves, typically used as guide mechanisms in cylinders and positioning platforms. Dovetail milling cutters are utilized for this process.

Keyway Milling
This is the process of forming keyways in workpieces, which serve as slots for fitting mechanical parts. Keyway milling usually involves using end mills and slot milling cutters.

Slotting and Slitting
This process involves making shallow and deep cuts in workpieces, employing tools like metal saws or specialized milling cutters.

Overall, these specialized milling grooving techniques enable the precise creation of various complex and purpose-specific grooves on workpieces.
Hole Milling
Milling machines can also perform drilling operations, creating holes with center drills followed by twist drills or end mills.
End mills are often used for holes requiring precision from the surface, as they can process both ends and holes without changing tools.
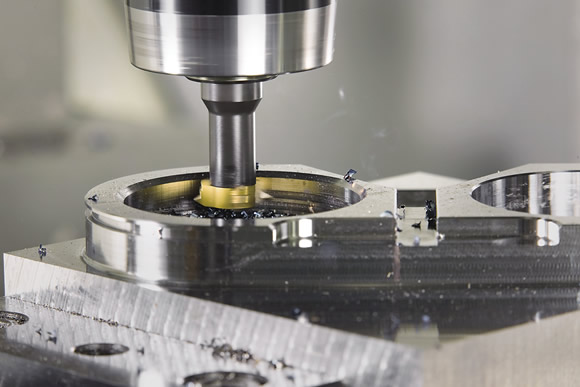
In summary, milling processes adapt to various shapes and precision requirements.
The choice of tool and machine type (vertical or horizontal) depends on the surface area and complexity of the task, balancing efficiency and precision for tasks ranging from flat surface machining to intricate slotting and hole drilling.
Common Problems and Treatment in Milling
In milling, achieving high precision requires understanding potential issues and how to address them. Here's a summary of common problems in milling and their solutions:
Vibration and Machining Defects
One of the frequent issues in milling is tool vibration, caused by vibrations from the machine tool or servo motor and variations in cutting force.
This vibration can lead to tool damage or machining defects. To prevent such issues, it's crucial to adjust cutting parameters, such as reducing cutting force, minimizing the number of cutting edges in contact, enhancing tool holder rigidity, and ensuring consistent tool protrusion to reduce load variations.
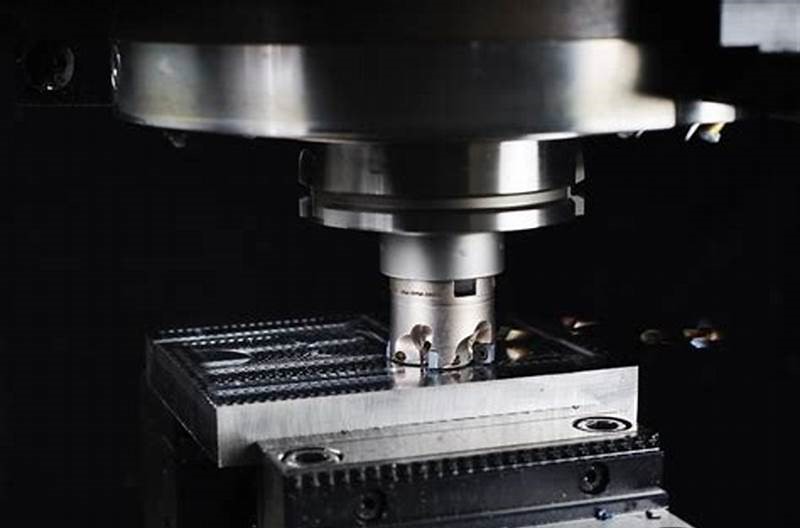
Excessive Tool Load
In milling, the tool is subjected to significant loads, resulting in severe tool wear.
Using a worn tool can cause poor machining, such as material degradation due to cutting heat or chip clogging.
Measures to prevent these defects include monitoring tool condition, using down milling methods, and employing tools with high-performance coatings.
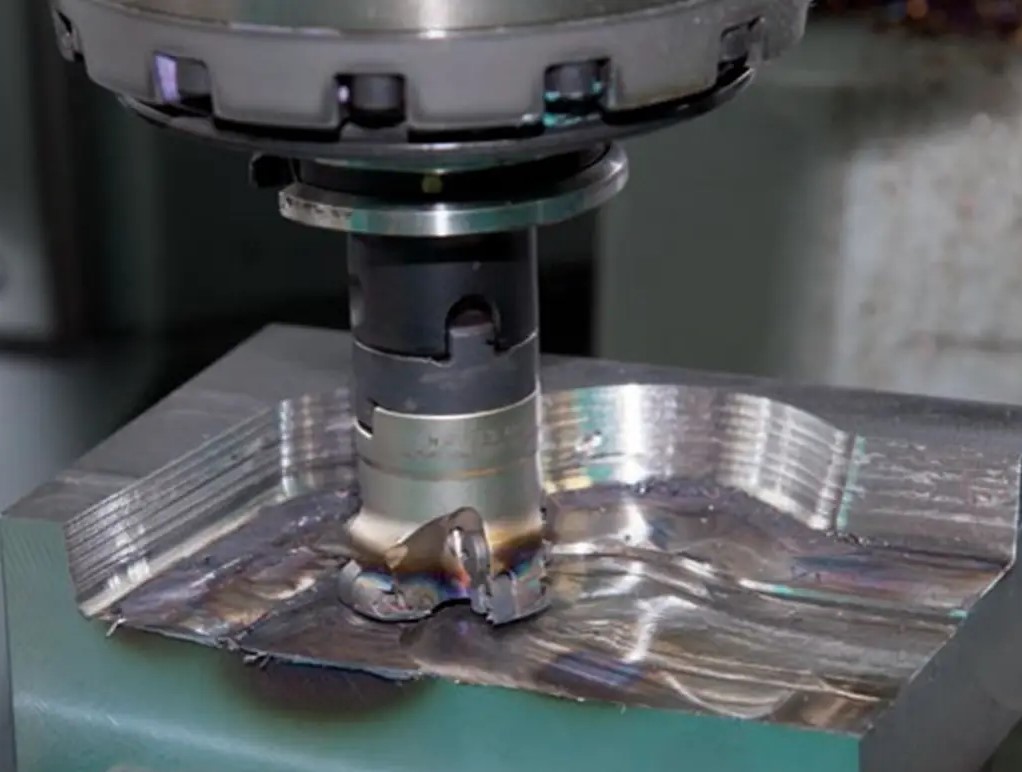
Challenges with Certain Shapes
Milling struggles with perfectly cornered machining, like sharp internal corners or "dovetail" cuts. Solutions involve designing parts that avoid these complex shapes or incorporating radii (R) or allowance in the design, like widened holes, to facilitate machining.
In summary, while milling allows for the precise machining of complex shapes, the choice of tools, adjustment of parameters, and design considerations are crucial.
Correct tool usage, parameter tuning, and design modifications are key to ensuring efficient and accurate milling processes.
With nearly 15 years of experience in CNC milling, santanoo can provide you with a variety of customized machining services.